HULK Metal is one of the sheet metal parts manufacturers in China. It has an advanced sheet metal manufacturing plant and can provide you with high-quality cutting, stamping, welding and assembly services.
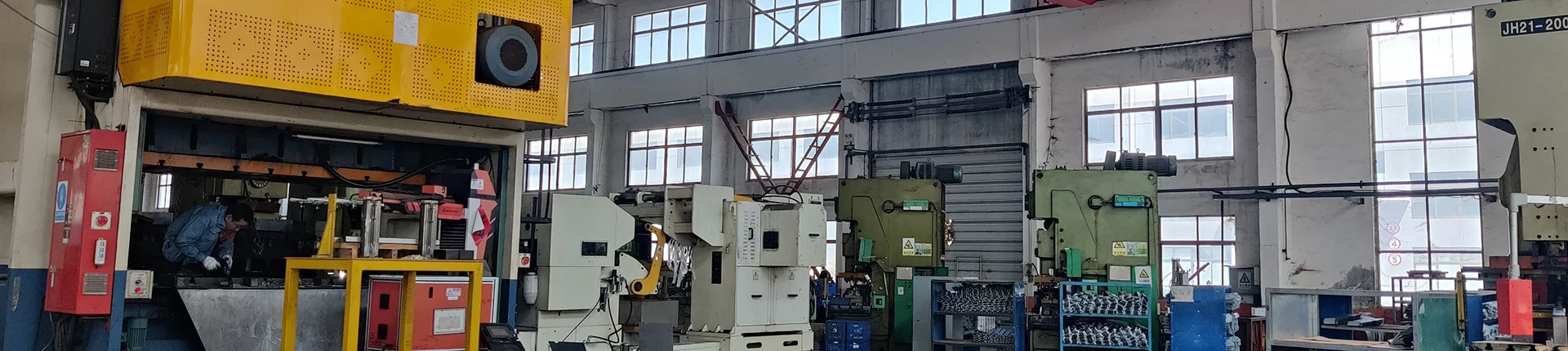
HULK Metal Stamping Factory Show
Sheet Metal Stamping Factory In China
HULK Metal Stamping Factory Show
HULK Metal: Advanced Equipment and Production Capacity Display of Sheet Metal Stamping Plant
Sheet metal stamping is an indispensable part of modern industrial manufacturing. The efficiency of its production process and product quality directly depend on the equipment level and management capabilities of the factory. As a professional enterprise in the field of sheet metal processing, HULK Metal not only has advanced production equipment, but also has rich industry experience, and can provide customers with high-quality sheet metal stamping services. This article will take you into HULK Metal's sheet metal stamping plant and introduce our production equipment and process flow in detail.
Cutting Area: Efficient And Precise Cutting Technology
In the early stage of sheet metal processing, cutting is one of the key processes. HULK Metal's cutting area is equipped with 5 laser cutting machines, which can meet a variety of production needs and ensure efficient and high-precision cutting operations.
The Role Of Laser Cutting Machine
Laser cutting machine cuts metal sheets quickly and accurately by focusing high-energy laser beams.
Versatility: It can be used to produce complete cut parts and can also complete the blanking process of some stamping parts.
High efficiency: Multiple laser cutting machines can run at the same time, supporting the cutting production of multiple batches of products.
High precision: Laser cutting machines can cut complex graphics and details, reducing the error of subsequent processing.
Case Display
Mass production: Multiple devices run at the same time, which can quickly complete the cutting task of large quantities of products.
Customized needs: Provide customers with high-precision cutting services for personalized parts.
Bending Area: Meet Bending Needs Of Different Specifications
In sheet metal processing, the bending process determines the shape and strength of the product. HULK Metal's bending area has 4 small bending machines and 2 large bending machines, which can cope with bending needs of different sizes and complexities.
Equipment Highlights
Multi-specification equipment combination: small bending machines are suitable for processing small-sized parts, while large bending machines can complete the bending of 3-meter-long metal plates at one time.
High-precision bending: CNC bending machines ensure the accuracy of bending angles and meet strict product quality requirements.
Process Advantages
High flexibility: The coordinated use of multiple bending equipment can quickly respond to different customer needs.
High-efficiency production: The bending process of large metal plates can be completed at one time, greatly shortening the production cycle.
Stamping Area: Stamping Equipment Of Various Tonnages
Stamping is the core process of sheet metal processing. HULK Metal's stamping area is equipped with punching equipment of various tonnages:
10 60-ton punching machines
5 110-ton punching machines
2 300-ton punching machines
2 510-ton punching machines
Flexibility In Equipment Selection
According to customer needs and product characteristics, we can flexibly choose suitable stamping equipment.
Light products: Use 60-ton and 110-ton punch presses to complete the processing of small and medium-sized parts.
Heavy products: 300-ton and 510-ton punch presses are suitable for processing thicker metal plates or complex structural parts.
Efficiency And Cost Control
Production efficiency: Multiple devices run simultaneously to achieve high efficiency in mass production.
Cost optimization: By reasonably selecting the tonnage of the punch press, both production quality and energy consumption and production costs can be guaranteed.
Typical Applications
Automotive parts: such as frame supports and reinforcements.
Industrial equipment parts: Processing of high-strength mechanical parts.
Welding Area: Perfect Combination Of Multiple Welding Processes
Welding process is an indispensable part of sheet metal processing. HULK Metal's welding area is equipped with a variety of welding equipment:
Laser welding machine
Argon arc welding machine
Resistance welding machine
Laser Welding Machine
High precision: It can achieve precise welding of parts and ensure that the weld is beautiful and firm.
High speed: Suitable for mass production and high-end precision parts processing.
Argon Arc Welding Machine
Wide application range: suitable for welding thin plates, stainless steel and other materials with high quality requirements.
High welding strength: ensure the service life of the product while meeting the appearance requirements.
Resistance Welding Machine
Suitable for mass production: efficient processing through fast welding.
Good stability: ensure the strength and uniformity of the product welding points.
Processing Area: High-Precision And Multi-Functional Processing
The processing area undertakes the hole processing and high-precision machining tasks of sheet metal products, equipped with:
Multi-hole processing machine
CNC processing center
Multi-Hole Processing Machine
High efficiency: complete the processing of 10 holes at one time, significantly shortening the production time.
High precision: ensure that the hole spacing and diameter of the porous parts meet the design requirements.
CNC Processing Center
High-precision processing: suitable for parts with complex shapes or high precision requirements.
Versatility: can complete multiple processes such as milling, drilling, tapping, etc., reducing the cost of transportation and secondary processing.
Assembly Workshop: Creating High-Quality Finished Products
In HULK Metal's assembly workshop, each processed component is assembled into a complete finished product.
Assembly Advantages:
Efficient assembly line operations ensure assembly quality and production efficiency.
Strict quality inspection process ensures that the finished product fully meets customer requirements.
Application areas: The assembly workshop provides services for multiple industries, such as automobiles, home appliances, industrial equipment, etc., to ensure the reliability and practicality of the products.
Quality Inspection Area: The Last Line Of Defense To Ensure Product Quality
Quality control is crucial in the entire production process of sheet metal processing. HULK Metal has set up a quality inspection area, equipped with advanced testing equipment and a professional quality inspection team, to strictly control each process to ensure that each product meets customer requirements.
Advanced Testing Equipment
Three-coordinate measuring machine
Used to accurately measure the geometric dimensions and shapes of products to ensure that key dimensions fully meet the design requirements of the drawings.
Hardness tester
Detect the hardness of metal materials to ensure the durability and reliability of products.
Welding flaw detector
Specially detects whether there are defects such as cracks and pores in the welding parts to ensure that the quality of the weld meets the standards.
Surface roughness meter
Used to evaluate the surface finish of the product to ensure that the appearance quality meets customer needs.
Multiple Quality Inspection Processes
Raw material testing
Material analysis is performed on each batch of raw materials to ensure that it meets the processing requirements and avoids the impact of material problems on production and product quality.
Process inspection
After each process such as cutting, bending, stamping and welding is completed, the quality inspector will conduct on-site inspections, including dimension measurement, welding inspection, etc., to find and solve problems in a timely manner.
Finished product inspection
After the product is assembled, a comprehensive quality inspection is carried out to ensure that the size, function and appearance meet the customer's final requirements.
Quality Inspection Advantages
Full process coverage: Quality inspection runs through every link from raw materials to finished products to ensure the stability and consistency of product quality.
Quick response: The quality inspection team can quickly discover and feedback problems to prevent defective products from flowing into the next process and improve production efficiency.
Compliance with international standards: The quality inspection process strictly complies with the requirements of the ISO 9001 quality management system to provide customers with high-quality sheet metal processing products.
Visit Our Factory: Transparent Production Process
HULK Metal always adheres to the principle of customer first, and welcomes customers to make an appointment to visit the factory at any time. Through field visits, customers can:
Fully understand our production capacity and equipment strength.
Communicate project details directly with the technical team to ensure seamless demand.
Enhance confidence in production quality and feel more at ease when placing orders with us.
HULK Metal's sheet metal stamping factory provides customers with efficient and high-quality processing services with advanced equipment and rigorous management processes. From cutting, bending, stamping to welding, processing and assembly, we pursue excellence in every link. Through a transparent production process, we are willing to work hand in hand with our customers to achieve a win-win situation.
If you are looking for a reliable sheet metal processing partner, please contact us and make an appointment to visit. We will serve you wholeheartedly!
Article Navigation
Article Navigation
Industries
Forging Factory
-
182024.10HULK Metal Fabrication
-
292024.10Introduction to Sheet Metal Forming: Processes, Materials, and Choosing the Right Partner
-
252024.10Comprehensive Guide to Sheet Metal Cutting: Methods, Materials, and Choosing the Right Partner
-
242024.10Comprehensive Guide to Sheet Metal Blanking
-
302024.09Comprehensive Understanding of Sheet Metal Welding